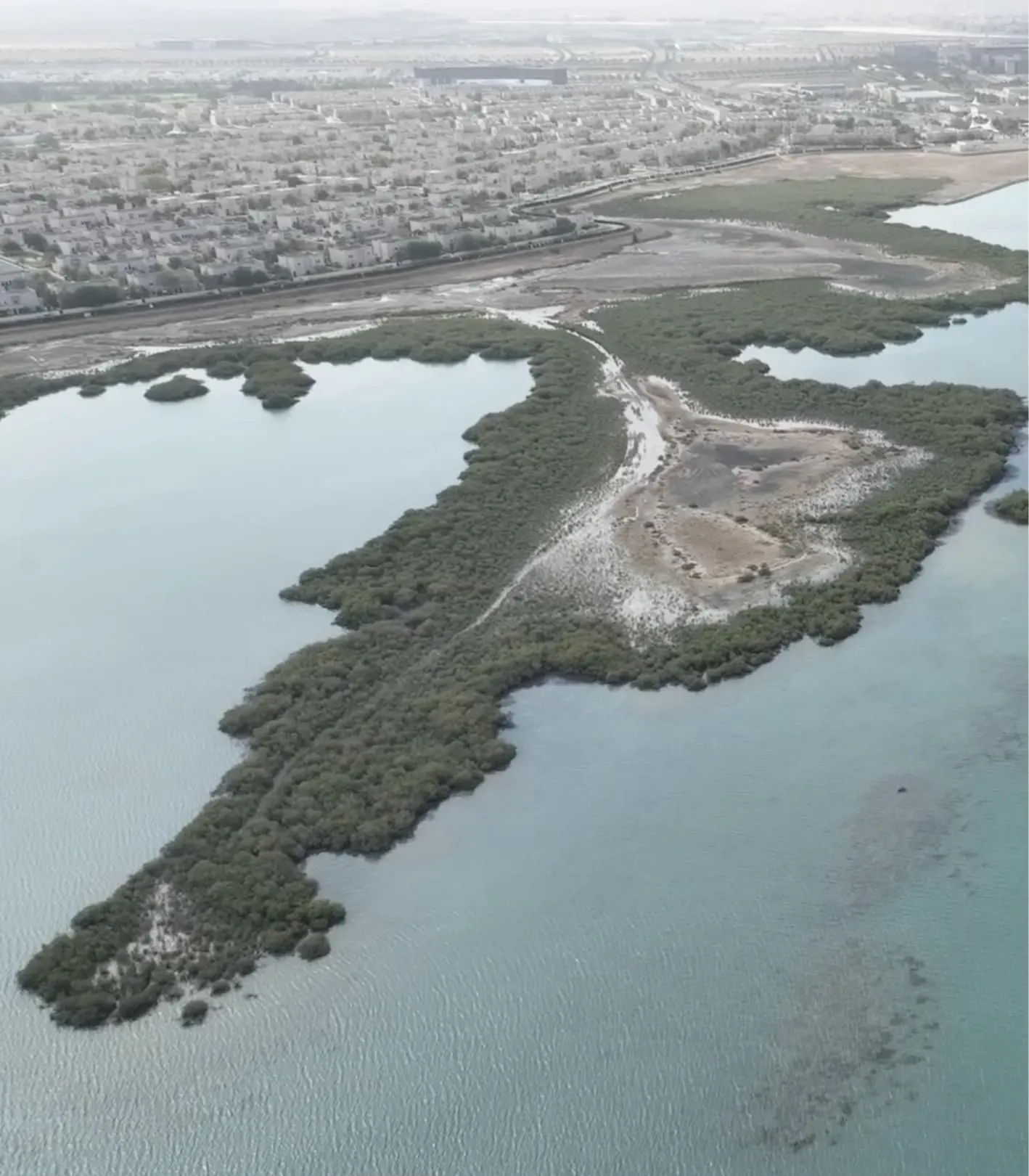
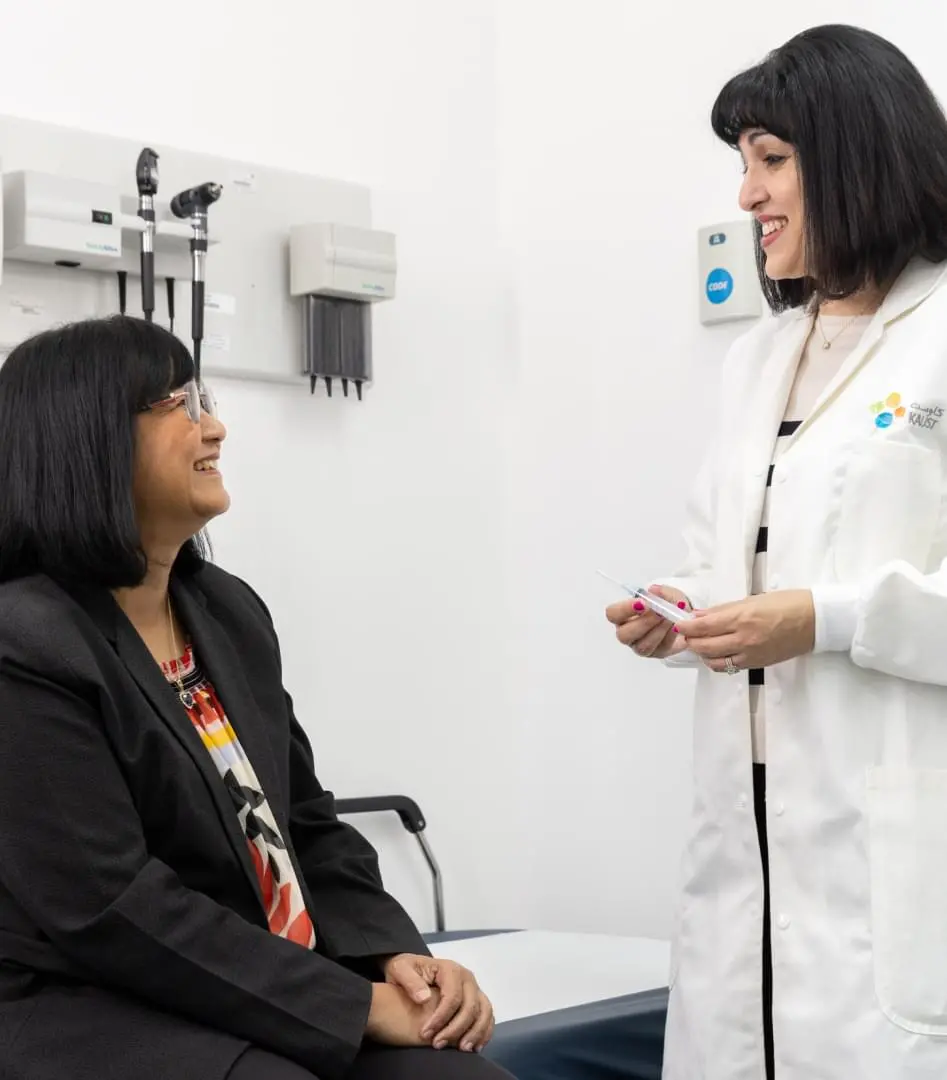
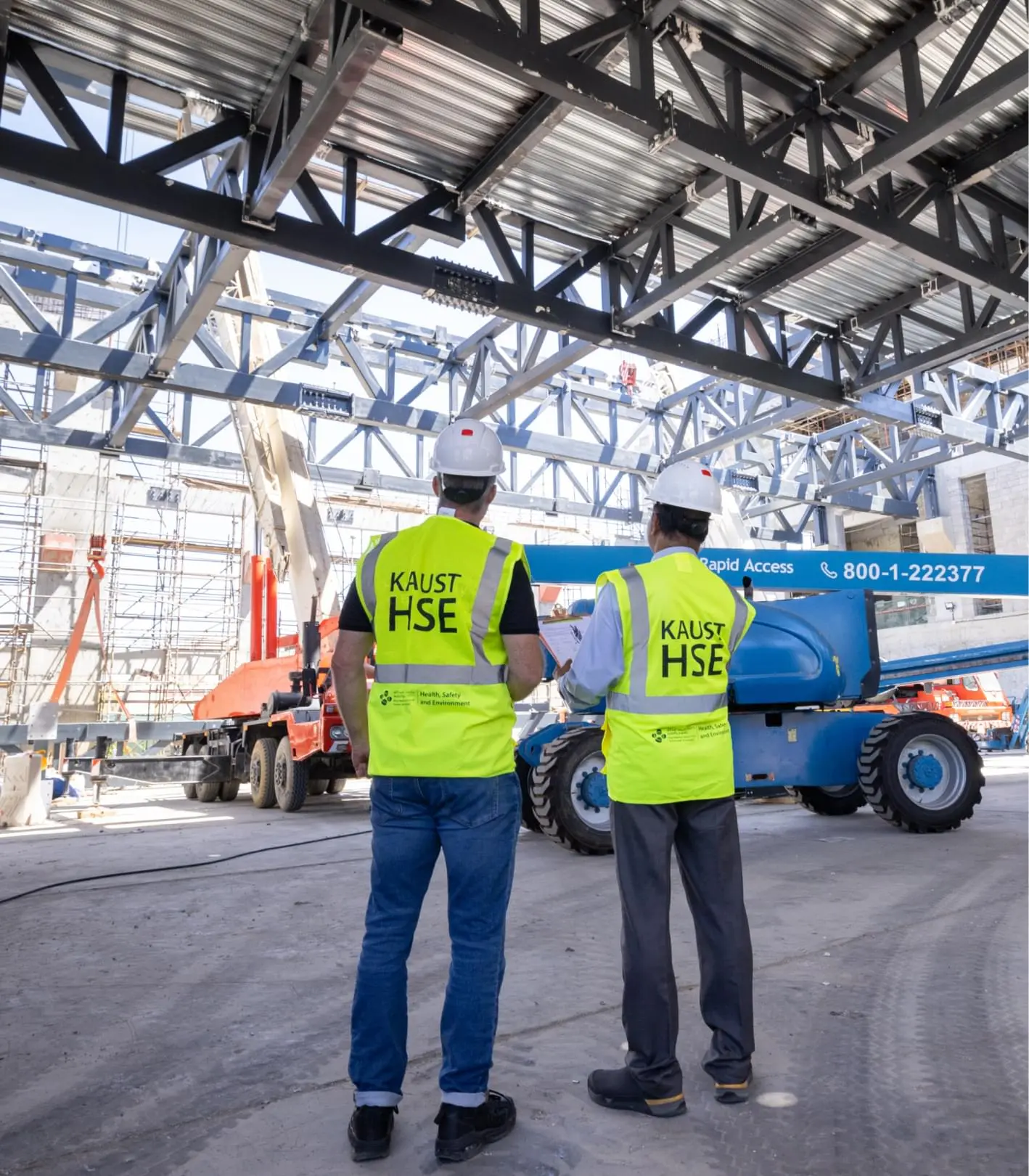
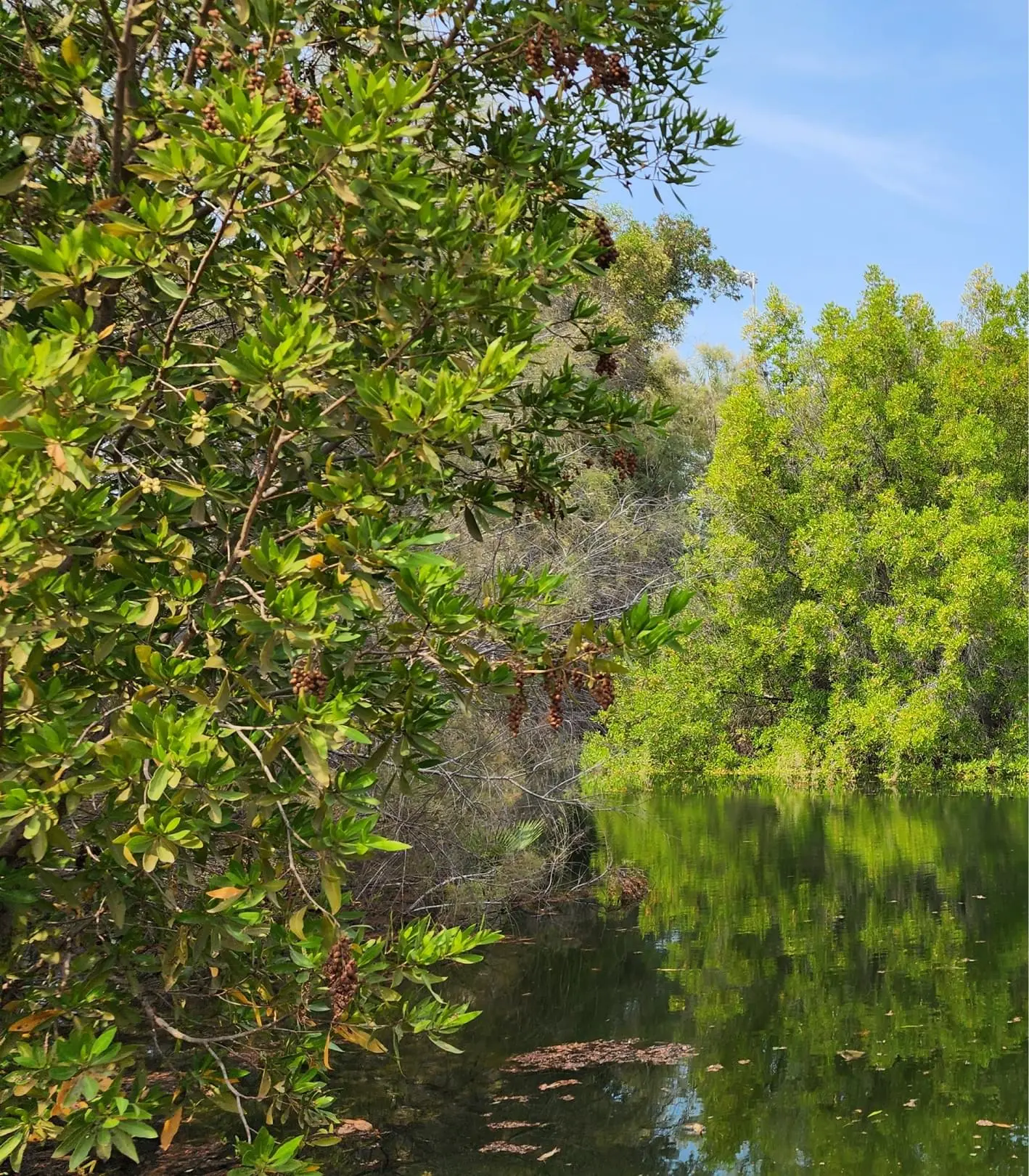
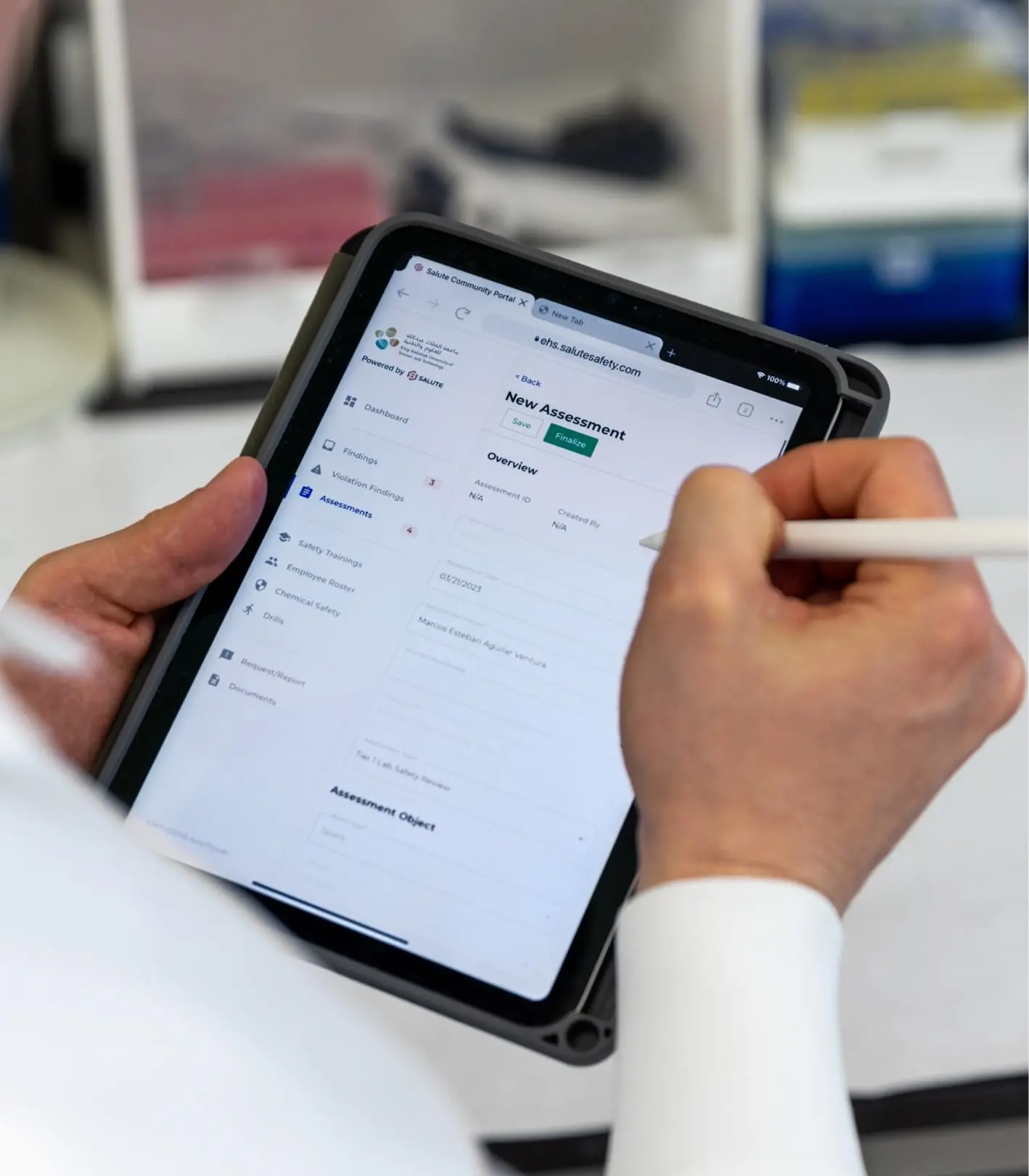
Quick Links:
A pressure vessel is a closed container designed to hold gases or liquids at a pressure substantially higher or lower than the ambient pressure.
Examples include glassware, autoclaves, compressed gas cylinders, compressors (including refrigeration), vacuum chambers and custom designed laboratory vessels Pressurized systems at can include
everything from small, unheated, low-pressure laboratory setups to large, extremely high-pressure heated metal vessels weighing several tons.
Pressure vessels, autoclaves and steam sterilizers operating at pressures greater than 100Kpa and larger than 140L volume elevate the risk and have stricter requirements for design, testing and approval.
The stored energy associated with these systems has the potential to cause injuries ranging from eye injuries to multiple fatalities and a pressure vessel as small as a few liters volume at 1400Kpa contains enough stored energy to cause fatal injuries.
The pressure differential between the inside and outside of the pressure vessel, whether created from chemical reaction, compressed gas, heating, chilling, cooling or vacuum, is a potential hazard. Many serious or fatal accidents have occurred when a pressure vessel or a component failed and generated flying projectiles or released hazardous materials. The primary causes of failure in pressurized metal vessels and components are fatigue cracking due to cyclic loading, overheating, and stress-enhanced corrosion cracking. Pressurized glass components typically fail as a result of corrosion, manufacturing and assembly stresses, and scratches on the glass surface due to improper handling. In both types of materials, failure can occur after a period of use at the originally designed pressure and temperature and without warning.
Pressurized systems must be designed to the ASME Boiler and Pressure Vessel Code by an engineer experienced in pressurized system design. Small low pressure laboratory setups and compressed gas distribution systems. Typically, it is best to purchase systems rather than design in- house. In all cases, it is best to work closely with the manufacturer of the components and materials to ensure that they are suited to the intended conditions of use.
Systems operating below 1 Megapascal, inert liquid (hydraulic) systems operating below 10 MPa. Total stored energy less than 100 kJ
Operates at gas pressures at or above 1 Megapascal, (MPa), operates at liquid pressures at or above 10 MPa gauge or contains over 100 kJ of stored energy.
Retain all manufacturer’s documentation related to environmental, temperature, and pressure ratings of each component in the system and
retain it with other written design specifications for future reference.
Limit the maximum allowable working pressure (MAWP), and temperature to that of the lowest rated component in the system.
Use the minimum size system possible to minimize the amount of stored energy.
Make sure all components, including soldered or brazed joints, in the system are rated for the chemical environment(s) to which they will be exposed.
Use pressure relief devices set at or below the MAWP of the system unless it is impossible to be over pressurized. A gas regulator is not a pressure relief device.
Isolate hazardous substances, components, and operations through the use of barricades, shielding, gas cabinets, or remote operation if the consequences of component failure or a process gas leak are unacceptable.
Do not subject glass equipment to pressure above atmospheric, except under the following conditions.
Specially constructed glassware for pressure use that is thoroughly shielded on all sides.
Pyrex “Double-Tough” glass pipe may be used at temperatures not exceeding 450 degrees Fahrenheit and pressures up to 50 psi in sizes through three inches.
All pressure vessels and piping must be constructed, repaired, altered, or tested according to the ASME Boiler and Pressure Vessel Code.
Protect all pressure equipment by adequate pressure-relieving devices that vent to a safe location.
Set safety or relief valves to blow at a pressure not to exceed the MAWP set for the intended operating temperature.
Be sure the capacity of the pressure-relieving device is sufficient to carry off the maximum quantity of liquid or gas that can be generated in or supplied to the attached equipment without permitting a rise in pressure in the vessel to more than 10 percent above the maximum allowable working pressure.
Take the nature of the vessel’s contents into account in the design of pressure-relieving devices.
Do not install a valve between a safety valve or similar device and the vessel being protected by it.
Test safety valves at frequent intervals.
Locate apparatus to be used under pressure only in areas specifically designed for that purpose.
Hydrostatic testing should be accomplished before equipment is placed in initial service. Hydrostatic testing should be re-accomplished every ten years thereafter, after significant repair or modification, or if the vessel experiences overpressure or over temperature.
Pressurized systems must be designed to the ASME Boiler and Pressure Vessel Code by an engineer experienced in pressurized system design. Small low pressure laboratory setups and compressed gas distribution systems. Typically, it is best to purchase systems rather than design in- house. In all cases, it is best to work closely with the manufacturer of the components and materials to ensure that they are suited to the intended conditions of use.
Do not use compressed air to clean clothing; the air jet tends to drive particles into the fabric, where they can cause skin irritation. Keep a clothes brush handy or, preferably, wear a lab coat.
Be sure no one is in the path of the air stream when using compressed air to dry mechanical parts. Always wear goggles or a face shield to protect your eyes.
Do not use air pressure to transfer liquids from containers. Use a siphon with a bulk aspirator or a pump instead. If a standard 208-L (55-gal.) drum is pressurized to 100 kPa (15 psig), the force exerted on the head of the drum is about 25 kN (3 tons). This is not an acceptable practice
Limit the transfer pressure of liquid nitrogen dewars to 100 kPa (15 psig).
Never apply air pressure to the body.
Unless an automatic shut-off coupling is used, attach a short chain (or equivalent) between a hose and an air-operated tool to prevent whipping in the event the coupling separates.
Unless an automatic shut-off coupling is used, vent the pressure in an air line before changing the nozzles or fittings.
Do not substitute compressed oxygen for air. Clothing saturated with oxygen burns explosively.
Threads on cylinder-valve outlet connections have been standardized by the Compressed Gas Association (CGA) and are not the same on all cylinders. This prevents accidental mixing of incompatible gases from an interchange of connections.
Left hand fittings for flammable and some oxidizing gases (some oxidizing gases use left hand thread, some do not) have a cut mark (notch) through the nut. Regardless, the notch indicates left hand thread.
Never lubricate, modify, force, or tamper with cylinder valves. Never put oil or grease on the high-pressure side of a cylinder containing oxygen, chlorine, or any oxidizing gas. An auto ignition or explosion could result.
Unlike larger cylinders, non-refillable lecture bottles have identical valve threads, irrespective of the gas contained within. Refillable lecture bottles use standard regulator fittings.
Threads on cylinder-valve outlet connections have been standardized by the Compressed Gas Association (CGA) and are not the same on all cylinders. This prevents accidental mixing of incompatible gases from an interchange of connections.
Where compressed gas containers are connected to a manifold, the manifold and its related equipment, such as regulators, shall be of proper design for the product(s) they are to contain at the appropriate temperatures, pressures, and flows.
Although glass vessels are frequently used in vacuum systems, they can explode or implode violently, either spontaneously from stress failure or from an accidental blow. Conduct pressure and vacuum operations in glass vessels behind adequate shielding.
Ensure the glass vessel is designed for the intended operation.
Carefully check glass vessels for star cracks, scratches or etching marks before each use. Cracks can increase the likelihood of breakage or may allow chemicals to leak into the vessel.
Seal glass centrifuge tubes with rubber stoppers clamped in place. Wrap the vessel with friction tape and shield with a metal screen. Alternatively, wrap with friction tape and surround the vessel with multiple layers of loose cloth, then clamp behind a safety shield.
Glass tubes with high-pressure sealers should be no more than 3/4 full.
Sealed bottles and tubes of flammable materials should be wrapped in cloth, placed behind a safety shield, then cooled slowly, first with an ice bath, then with dry ice.
Never rely on corks, rubber stoppers or plastic tubing as pressure-relief devices.
Glass vacuum desiccators should be made of Pyrex or similar glass and wrapped partially with friction tape to guard against flying glass. Plastic desiccators are a good alternative to glass, but still require shielding.
Never carry or move an evacuated desiccator.