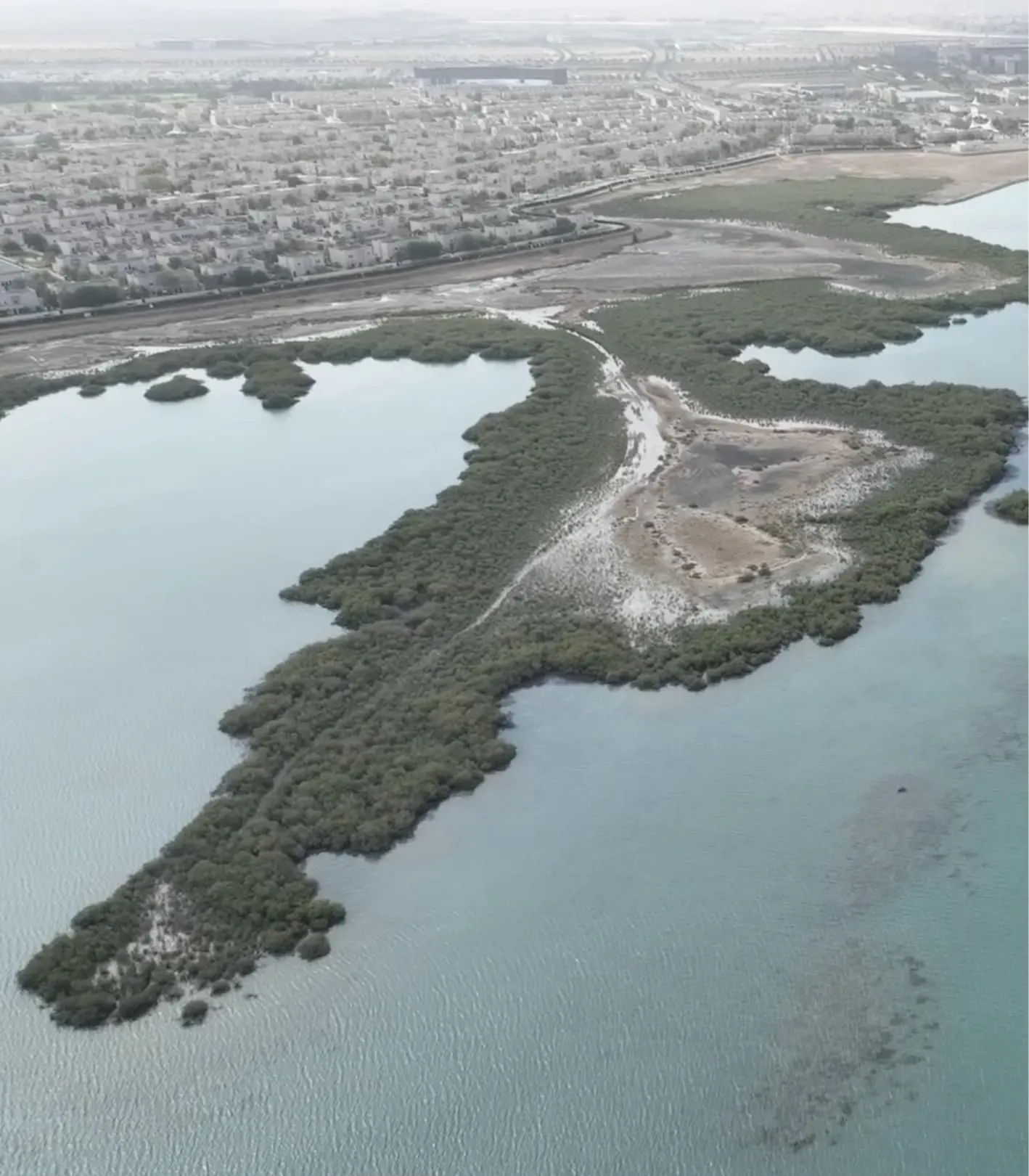
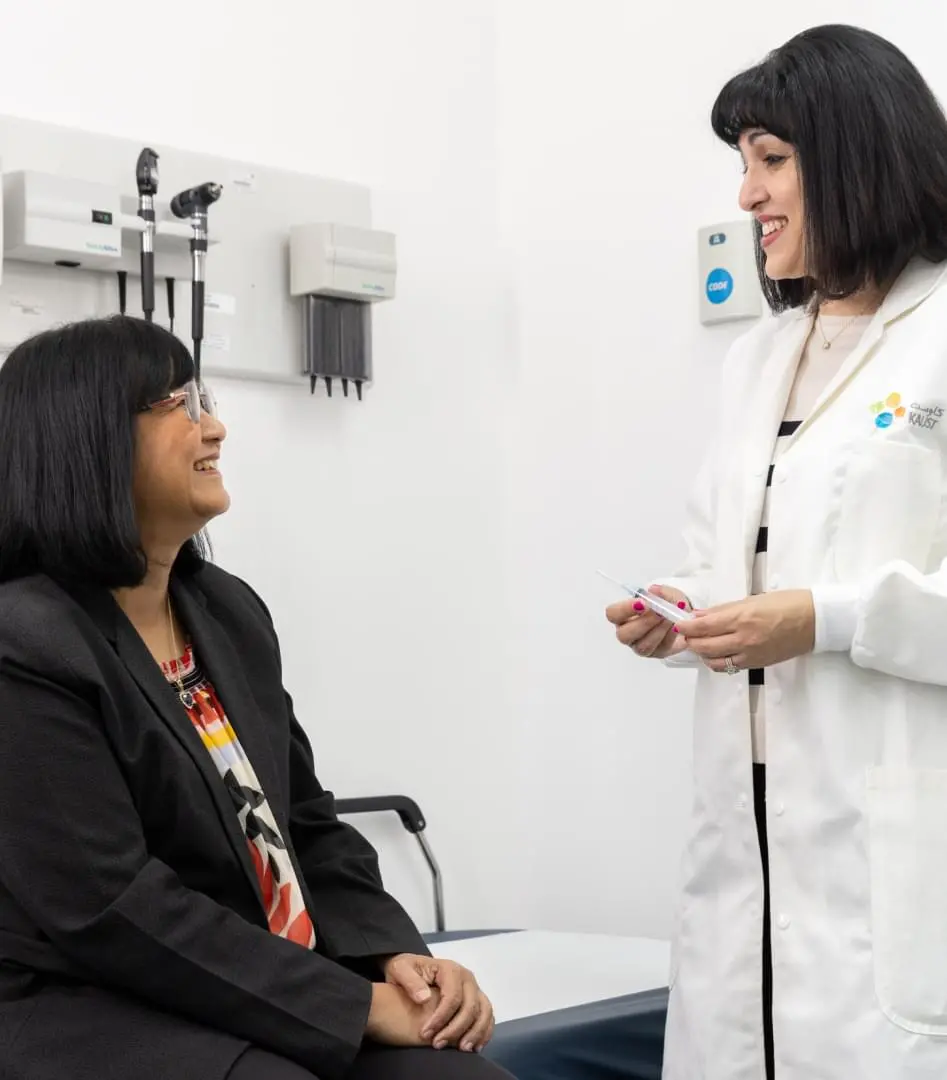
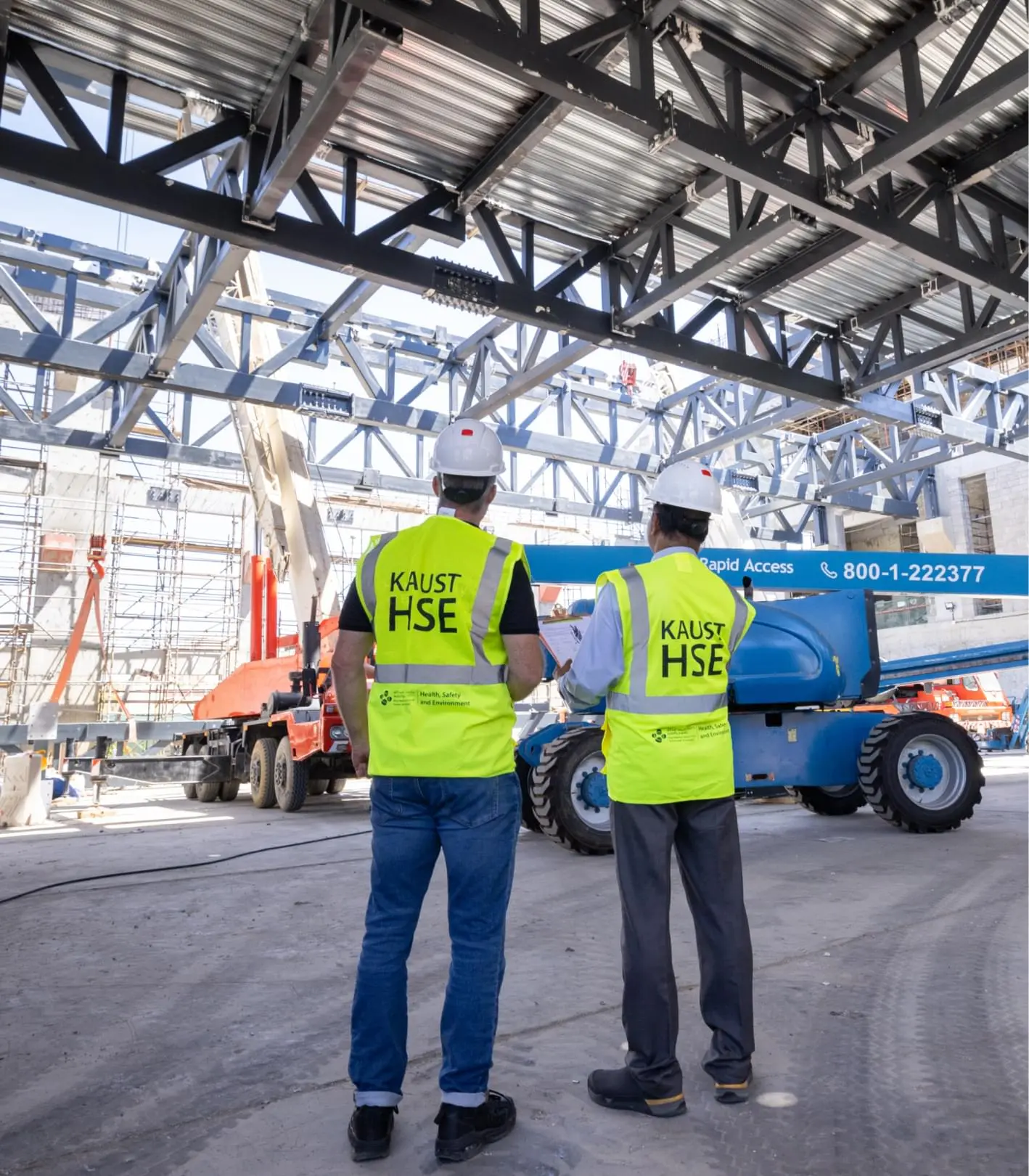
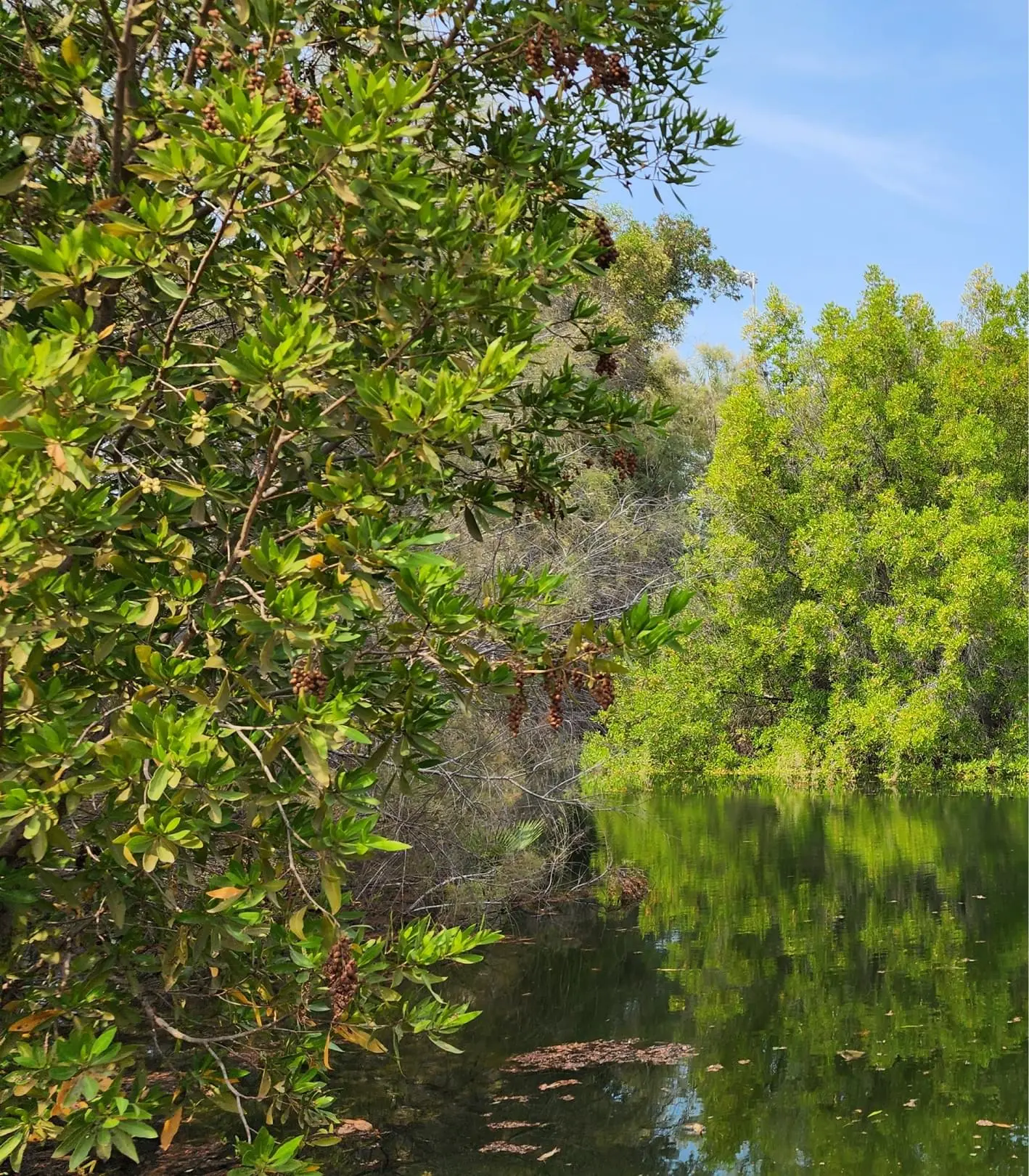
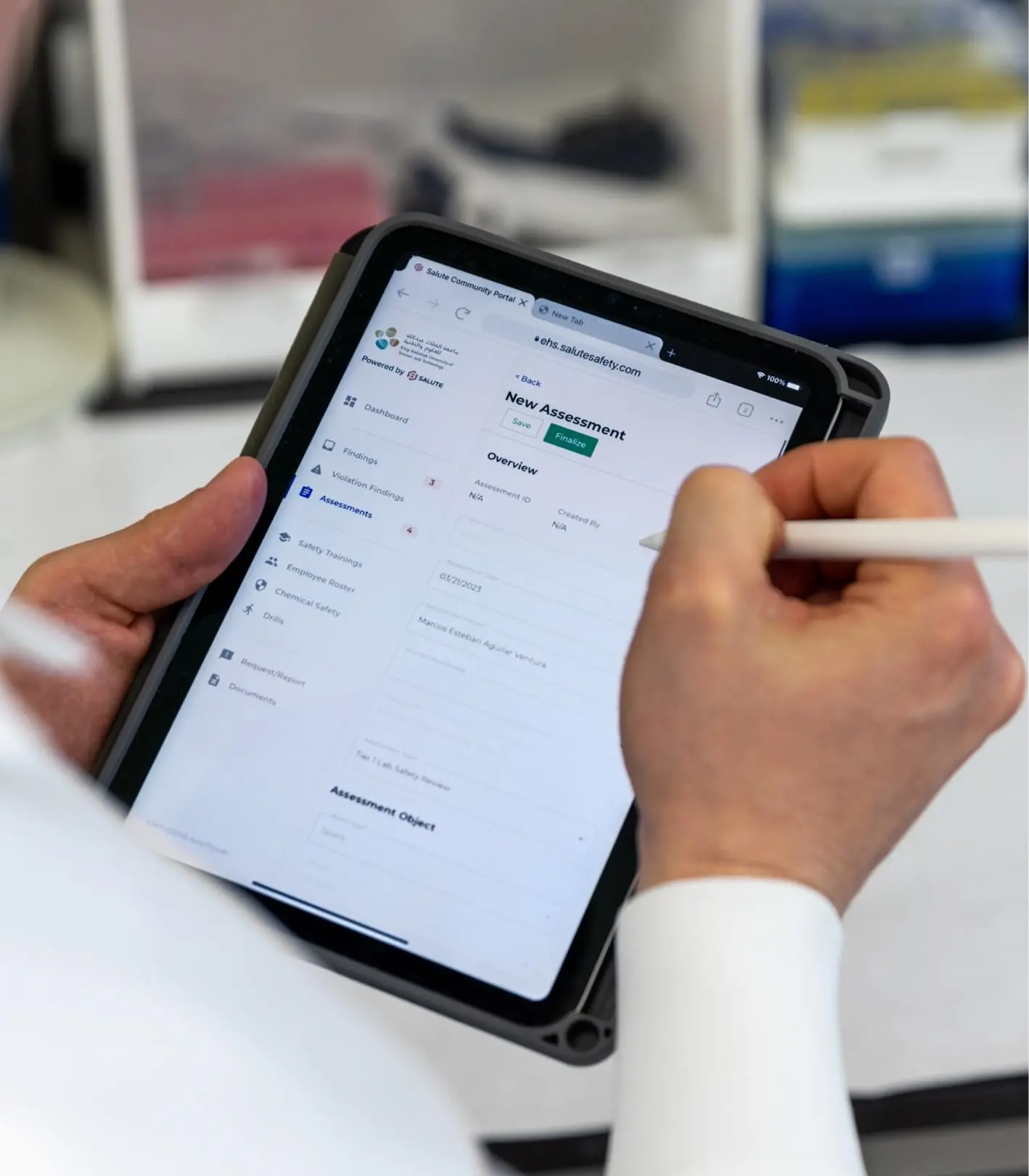
Quick Links:
Administrative controls include policies and procedures that result in providing proper guidance for safe laboratory work practices and set the standard for behavior within the laboratory. Once developed, administrative controls must be implemented and adhered to by all personnel working in the laboratory. Laboratories are responsible for developing policies and written guidelines to ensure laboratory workers are protected against exposure to hazardous chemicals as outlined in the Occupational Health and Safety Administration, USA (OSHA) Laboratory Standard and physical hazards that may be present, including the development of a written Chemical Hygiene Plan or adoption of this Laboratory Safety Manual. It is the responsibility of the Principal Investigator and laboratory supervisor to ensure that personnel working in laboratories under their supervision are informed and follow laboratory specific, departmental, and campus wide policies and procedures related to laboratory safety – such as the guidelines and requirements covered in this Laboratory Safety Manual.
Whenever possible, laboratory personnel should avoid working alone when conducting research, especially when experiments involve hazardous substances and procedures. Laboratories should establish specific guidelines and standard operating procedures specifying when working alone is not allowed and develop notification procedures when working alone occurs. All work to be performed by someone working alone, and the monitoring system that is established, must be approved in advance by the Principal Investor or laboratory manager.
If a laboratory person determines it is necessary to work alone, consideration should be given to notifying someone else in the area – in an adjacent room, another lab on the same floor, or a lab on a different floor. It is recommended that a “buddy system” be established for regular, routine checks on personnel working alone, such as every 15 – 30 minutes, to ensure no accidents have occurred. This could be accomplished by physically walking to the room where the lab worker is, or through the use of a phone. If the person working alone is doing highly hazardous work, then the person checking on the lab worker should not enter the same room. A system of visual checks should be established to indicate there are no problems or to determine if help is needed.
Chemical fume hoods are installed in laboratories to protect individuals from airborne substances (gases, vapors, mists, fumes) generated by laboratory experiments. However, simply conducting these experiments in the fume hood does not guarantee adequate protection. The fume hood must be used properly.
Each laboratory is required to have a written Laboratory Safety Plan to help protect against hazards to personnel, property, or the environment:
The Laboratory Safety Plan should outline the lab-specific practices and procedures, personal protective equipment, training requirements, standard operating procedures, emergency procedures, and other safety requirements to protect employees from the hazards they may encounter in the laboratory.
The Laboratory Safety Plan must be submitted to HSE upon initial completion and reviewed annually or whenever there is a significant change in laboratory operations and/or hazards present, or a change in emergency contact personnel.
It is the responsibility of the Principal Investigator to ensure a Laboratory Safety Plan is written and that all personnel working in laboratories under their supervision have reviewed and understood the plan.
Laboratories are responsible for developing Standard Operating Procedures (SOPs) for any processes or operations that involve the use of any hazardous chemical, biological, radiological, equipment or other hazardous processes or operations..
SOPs can be stand-alone documents or supplemental information included as part of research notebooks, experiment documentation, or research protocols. The requirement for SOPs is to ensure a process is in place to document and address relevant health and safety issues as part of every experiment. Here you can find list of guidelines to follow for drafting specific SOPs
SOPs do not need to be lengthy or wordy dissertations and it is perfectly acceptable to point laboratory personnel to other sources of information.
“To use this piece of equipment, see page 4 in the operatorʼs manual (located in file cabinet #4).” “The chemical and physical hazards of this chemical can be found in the SDS – located in the SDS binder. Read the SDS before using this chemical.” “When using chemical X, wear safety goggles, nitrile gloves, and a lab coat.”
HSE can assist laboratories with developing general and specific SOPs. Due to the variety of research and the large number of laboratories on the KAUST campus, it is the responsibility of each Principal Investigator to ensure that SOPs are developed and the practices and procedures are adequate to protect lab workers who are exposed to any chemical, biological, radiological, or physical hazards.
It is the responsibility of the Principal Investigator and laboratory manager to ensure written SOPs incorporating health and safety considerations are developed for work involving the use of hazardous chemicals in laboratories under their supervision and that PPE and engineering controls are adequate to prevent overexposure. In addition, Principal Investigators and laboratory managers must ensure that personnel working in laboratories under their supervision have been trained on those SOPs.
Keep all areas of the lab free of clutter, trash, packaging, extraneous equipment, and unused chemical containers. Areas within the lab that should be addressed include benches, hoods, refrigerators, cabinets, chemical storage cabinets, sinks, trash cans, etc.;
Aisles and hallways shall have proper egress and a minimum clearance of one meter (three feet). Do not block or impede exit ways or doors. See the Service Corridor Policyfor more information;
Clean up all chemical spills immediately, regardless if the chemical is hazardous or not. When cleaning up a chemical spill, look for any related splashes on nearby equipment, cabinets, doors, and counter tops;
Keep areas around emergency equipment and devices clean and free of clutter. This includes items such as eyewash/emergency showers, electric power panels, fire extinguishers, and spill cleanup supplies;
Keep a minimum of one meter or three feet of clearance (as required by fire codes) between benches and equipment. Exits must be clear of obstacles and tripping hazards such as bottles, boxes, equipment, electric cords, etc. Combustible materials may not be stored in exits (including corridors and stairways), exit enclosures, or mechanical electrical equipment rooms;
When storing items overhead, keep heavier and bulkier items closer to the floor. In sprinklered rooms, all storage, including both combustible and non-combustible materials, must be kept at least 45 centimeters (18 inches) below the level of the sprinkler head deflectors to ensure that fire sprinkler coverage is not impeded;
Keep all containers of chemicals and waste closed when not in use.
It is the responsibility of Principal Investigators and laboratory managers to ensure laboratories under their supervision are maintained in a clean and orderly manner and personnel working in the lab practice good housekeeping.
Whenever it is necessary to have unattended operations occurring in a lab, it is important to ensure safeguards are put into place in the event of an emergency. Laboratory personnel should adhere to the following guidelines when it is necessary to carry out unattended operations. For unattended operations involving highly hazardous materials, an appropriate warning/explanation sign should be placed on the laboratory door, or in a conspicuous place that could be easily seen without putting someone else in danger in the event of an emergency.
When setting up an experiment that will be left unattended, try to take into account potential incidents that could occur if something went wrong.
Access to KAUST University laboratories, workshops and other work areas housing hazardous materials or machinery is restricted to the relevant University faculty, staff, students, or other persons on official business. Visitor guidelines, visiting scientists, open houses and tour guidelines are published on this page.
Pets are prohibited in KAUST laboratories. In addition, while on University- controlled property, animals must be attended and restrained at all times.
It is the responsibility of the center directors, Principal Investigators, and laboratory managers to ensure visiting scientists and other similar users have been properly trained and made aware of any potential health and physical hazards that may exist in their labs.
To prevent exposure to hazardous materials through ingestion, do not eat, drink, chew gum, or apply cosmetics in areas where hazardous materials are used. Wash your hands thoroughly after using any chemicals or other laboratory materials, even if you were wearing gloves, and especially before eating or drinking.
To help promote awareness, laboratories refrigerators and freezers should be properly labeled. Refrigerators used for the storage of chemicals should be labeled “Chemicals Only, No Food”. Examples of these signs can be found on the Signs and Labels webpage.
Keep in mind that some chemical exposure can result in immediate effects (acute exposure) while other effects may not be seen for some time despite repeated exposure (chronic exposure). Consuming food or drink or applying cosmetics in the lab can result in both types of exposure.
Good chemical hygiene practices include the use of personal protective equipment (PPE) and good personal hygiene habits. Although PPE can offer a barrier of protection against chemicals and biological materials, good personal hygiene habits are essential to prevent chemical exposure, even when using PPE.
Do not eat, drink, chew gum, or apply cosmetics in a lab or other area where chemicals are used.
Do not store food or drink in refrigerators that are used to store chemicals.
Do not ever try starting a siphon or pipette by mouth, doing so can result in ingestion of chemicals or inhalation of chemical vapors. Always use a pipette aid or suction bulb to start a siphon.
Always confine long hair, loose clothing, and jewelry.
Wear a lab coat when working with hazardous materials.
Shorts, skirts, sandals, and open toed shoes are not permitted in KAUST laboratories.
Remove laboratory coats, gloves, and other PPE immediately when chemical contamination occurs. Failure to do so could result in chemical exposure.
After removing contaminated PPE, be sure to wash any affected skin areas with soap and water for at least 15 minutes.
Always remove lab coats, scrubs, gloves, and other PPE before leaving the lab. Do not wear lab coats, scrubs, or other PPE (especially gloves) in areas outside the lab, particularly not in areas where food and drink are served, or other public areas.
Always wash hands with soap and water after removing gloves and before leaving the lab or using items such as the phone, turning doorknobs, or using an elevator.
Always wash lab coats separately from personal clothing. Be sure to identify contaminated lab coats to commercial laundry facilities to help protect their workers by placing the contaminated lab coat in a separate plastic bag and clearly identifying the bag with a note or label indicating the lab coat is contaminated.
The following are guidelines designed to minimize opportunities for intentional removal of any hazardous materials from your laboratory:
Recognize that laboratory security is related to, but different from laboratory safety. Security is preventing intrusion into the laboratory and the theft of equipment or materials from the lab.
Develop a site-specific security policy. Make an assessment of your laboratory area for hazardous materials and particular security issues. Then develop and implement lab security procedures for your lab group and train lab group members on security procedures and assign responsibilities.
Control access to areas where hazardous chemicals are used and stored. Limit laboratory access to only those individuals who need to be in the lab and restrict off-hours access only to individuals authorized by the Principal Investigator.Be sure to lock freezers, refrigerators, storage cabinets, and other containers where stocks of biological agents, hazardous chemicals, or radioactive materials are stored when they are not in direct view of workers (for example, when located in unattended storage areas). Do not leave hazardous materials unattended or unsecured at any time. Most importantly, close and lock laboratory doors when no one is present.
Know who is in the laboratory area at any given time. Approach anyone who you donʼt recognize and appears to be wandering in laboratory areas and hallways and ask if you can help direct them.
Secure your highly hazardous materials. Consider using a log to sign hazardous materials in and out of secure storage and be sure to take a periodic inventory of all highly hazardous chemicals, biological agents/toxins, and controlled substances (this is required for use of radioactive materials). This could be as simple as frequently looking at your chemical containers to be sure that none are missing. Report any missing inventory to KAUST security immediately.
Know what materials are being ordered and brought into the laboratory area. Visually screen packages before bringing them into your lab. Packages containing potentially infectious materials should be opened in a biological safety cabinet or other appropriate containment device. Know what materials are being removed from the laboratory area and consider tracking the use and disposal of hazardous materials.
Pay special attention to the following:Open labs Unrestricted access to toxic chemicals Unlocked support roomsToxic gas security Unsecured biological materials and waste Access to controlled substances
Evaluation and assessment of risk is an integral step in designing an experimental protocol. Not only does a thorough risk assessment allow researchers to systematically identify and control hazards, but also improves science through better planning and understanding of the research question and variables.
Contact HSE@kaust.edu.sawith any questions or to request support in conducting a risk assessment.
The Risk Assessment Tool uses a four-part framework that can be used for an experiment, analytical process, or series of tasks:
Determine the scope of your work, beginning with your research objective. What scientific question(s) are you trying to answer or problem(s) are you trying to solve? Conduct a broad review of the literature. Consider querying other disciplines. Talk with others who have done similar work.
Outline your procedure/tasks. This may include a deeper dive into specific topics in the literature. Determine hazards associated with each step/task and the control measures for reducing risk. HSE can help with more detailed guidance on how to control certain hazards.
What assumptions did you use? Question the importance of each step. Seek advice from others to challenge your thinking. Ask yourself “what could go wrong?” Assign a risk rating (revising steps or controls particularly if risk category is “high” or “unacceptable”). HSE can provide experimental design review to help with this process.
Implement a model, prototype, or trial run. Can you perform a dry run to familiarize yourself with equipment and procedures? Can you test your experimental design at a smaller scale or with a less hazardous material? Determine if any design changes are needed. Run your experiment and monitor how your controls perform. Assess as you go and make changes as necessary.
All researchers should conduct a risk assessment prior to conducting an experiment for the first time. When repeating an experiment/process, researchers may refer to a previous risk assessment and update the “Evaluate” section with the findings. The risk assessment process involves rating the risk of the experiment, from low to unacceptable risk. Consult with your PI/supervisor and HSE if your risk rating is “high” or “unacceptable” to redesign the experiment and/or implement additional controls to reduce risk.
PIs and LSR should review risk assessments conducted by lab personnel/researchers. When personnel identify a “high” or “unacceptable” risk, PIs must work with them to redesign experiments or implement controls to reduce risk. If the risk rating remains “high” or “unacceptable” after redesign, consult HSE to provide guidance to control hazards.
In addition to review of risk assessments, PIs are also encouraged to use the risk assessment framework during group meetings to discuss planned or completed experiments.
Risk Assessments and Standard Operating Procedures (SOPs) are complementary tools. An SOP is typically written for repeated operations, equipment use, or required maintenance. SOPs may also be required for high-hazard chemicals and operations (e.g. work involving particularly hazardous substances, hihly reactive chemicals, and other high risk research procedures).
A Risk Assessment is well-suited to novel operations in which the researcher is designing and planning an experiment. However, the Risk Assessment Tool can also be helpful in understanding risk when preparing for procedures that have an established SOP, varying parameters (e.g. scale, reagents, conditions), or in preparing to write new SOPs.